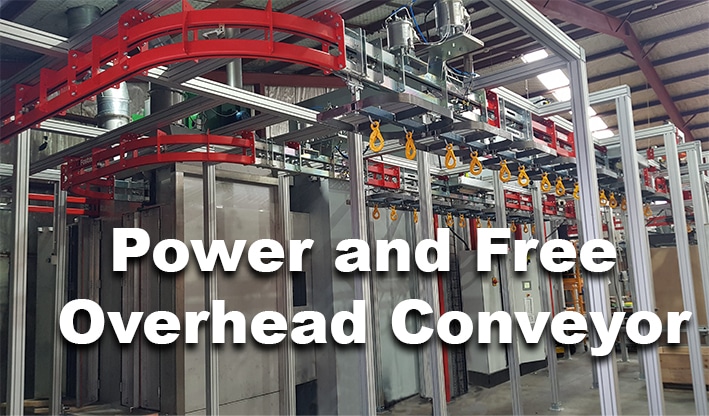
With space at a premium in any manufacturing and warehousing facility, moving production, processing and storage to an overhead conveying system makes a lot of sense – both financially and logistically. It’s a move that will both improve productivity and provide a safer, more pleasant and more efficient working environment.
Incredibly powerful and efficient, overhead conveyors have applications in many industries – from simple paint lines to complete online manufacturing and distribution centres.
JIPL have designed and supplied overhead conveyor systems for companies like OBO, Altus and Temperzone to name a few. JIPL’s solution for OBO trebled the plant’s capacity and is achieving consistent quality throughout the plant. These solutions for our clients have solved key business issues and increased throughput.
The key benefits of overhead conveying systems over floor level systems include:
- Allowing variable workflow & online manufacturing
- Excellent control of production & inventory
- Reduction of inventory & storage areas required
- Maximising plant usage by freeing up floor space
- Removing clutter and associated safety issues from the floor area
- Reduction in product damage and rework due to floor trolley banging etc.
- Optimising of product accessibility for workers
- Reducing bending and lifting involved for workers
An overhead conveyor consists of an overhead track and chain, and objects are suspended from the chain to be transported along the path of the track. The machinery for overhead conveyors is mounted near the ceiling, away from workers and equipment. This reduces noise levels and safety concerns about pinch points and careless workers, plus the conveyor does the lifting, which reduces worker injuries & claims.
The product travels a fixed path and is less likely to be damaged by accident than if transported on the floor.
Overhead conveyors are also the most flexible of materials handling systems and are ideally suited to an enormous range of transfer and processing operations. For the transfer of product from one factory area to another, overhead conveyors can be routed at a high level, leaving valuable working space free for production. Carrying capacities are amazing: up to 12 tonnes per pendant, though most operate in the 10 – 250kg per pendant range, with speeds of up to 20 metres per minute.
For more complex operations, the Power and Free overhead conveyors are simply incredible – they can not only go around and around, up and down, and upside down, but they can also perform an enormous variety of tasks – from individual components, pallet loads of goods, batches of goods, through to bags and boxes.
Importantly, the system can grow with the growth of the business and automation can be added as growth and/or the need for improved productivity dictates. When designing an overhead conveyor system, speed, capacity, workflow and facility layout must be considered. A facility can be redesigned by breaking up a linear process into more efficient subassembly workstations, instituting ‘just-in-time’ methods and can ultimately eliminate current inventory storage completely.
Because an overhead conveyor system can have an impact on the way things are done, it should be approached as part of an overall strategic process and operation redesign. JIPL provides design options, ancillary equipment, control systems, installation, and commissioning.