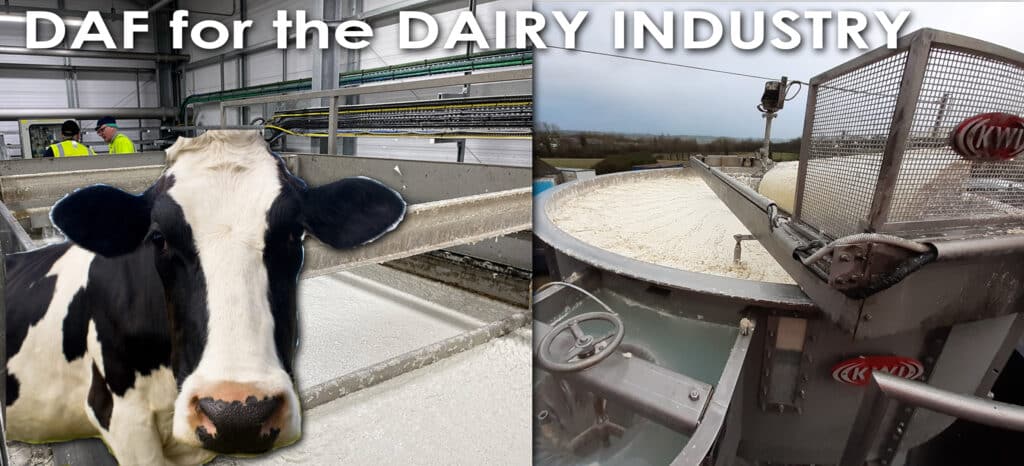
Dissolved Air Flotation (DAF) technology answers the need for heightened environmental responsibility in the dairy industry.
In the quest for continuous innovation and sustainable practices, the dairy industry is experiencing a transformative shift propelled by cutting-edge technologies. The pioneering use of Dissolved Air Flotation (DAF) technology is a revolutionary approach that addresses critical challenges in dairy processing, wastewater management, and environmental impact.
Enhancing Dairy Processing
Traditional dairy processing methods often generate substantial amounts of wastewater laden with organic matter, fats, and proteins. This wastewater not only poses environmental concerns but also affects operational efficiency. Here, DAF technology emerges as a game-changer. By effectively removing suspended particles, fats, and proteins, DAF ensures cleaner water discharge while potentially allowing the recovered materials to be reused or converted into value-added products like biogas or fertilizers.
JIPL works with the KWI Group, global leaders in water and wastewater treatment technologies, to provide cost-effective wastewater treatment in New Zealand.
Most of the DAF plants used in the dairy industry in New Zealand tend to be very large tank-type old technology. The KWI DAF technology has a significantly smaller footprint and is more effective.
The KWI Group is one of the pioneers of Dissolved Air Flotation (DAF) technology and is one of the oldest existing DAF unit manufacturers in the world. The KWI DAF range includes 11 standard models and custom designs to meet all customer requirements. With nearly 70 years of experience and the supply of 7000 DAF units for 5000 references globally, the KWI Group is strategically qualified to serve process industries worldwide with quality and lasting equipment. KWI boasts the broadest range of DAF products of any provider in the global arena.
Advantages of KWI DAF
- Small footprint
- Less energy and chemical consumption
- High sludge concentration: up to 5% of solid content
- Allows efficient and optimal polymer dosing, therefore minimising the polymer consumption
JIPL offers KWI’s DAF solutions in New Zealand tailored to a wide variety of dairy operations. DAF technology is effective for the comprehensive treatment of diverse dairy contaminants found in products such as cheese, yoghurt, ice cream, cream, butter, and milk.
Different effluent requires different technology for effective treatment, and the KWI Group offers an extensive range of solutions to meet every dairy customer’s unique requirements. These include the Ecocell, Minicell, Megacell, and Supracell DAF systems.
KWI (UK) Ltd has recently introduced the Supracell. This was originally designed for applications in the pulp and paper sector. However, its remarkable adaptability has extended its utility to various industries, including the dairy sector.
The compact dimensions of the Supracell render it an optimal choice for dairy sites constrained by space considerations. Recognizing the preference for turnkey solutions among many clients grappling with effluent treatment issues, KWI (UK) Ltd now offers the Supracell as a skid-mounted unit. This comprehensive solution arrives pre-wired, tested, and can be seamlessly deployed with minimal on-site installation requirements.
For Arla Food’s new creamery in Stourton KWI provided a Megacell MCH DAF clarifier for complete treatment for direct discharge to sewer. The valuable fats are removed and recovered by the DAF plant (without any chemical additions). Further processing with effluent from other parts of the plant is done using a second DAF plant.
The use of a KWI Minicell (MNC) effectively addresses the removal of phosphates and reduction of COD from mozzarella production operations in Glanbia Cheeses in Anglesey. Here, effluent from the sump is channelled through a rotary screen installed by KWI UK Ltd, onward to an aerated balancing tank, and finally to the DAF through an MNC skid. The ensuing clarified water is discharged directly or can be reintroduced to the balance tank if needed. The DAF sludge follows a controlled discharge process to a transfer tank, eventually progressing to a 25m3 decant tank for further thickening.
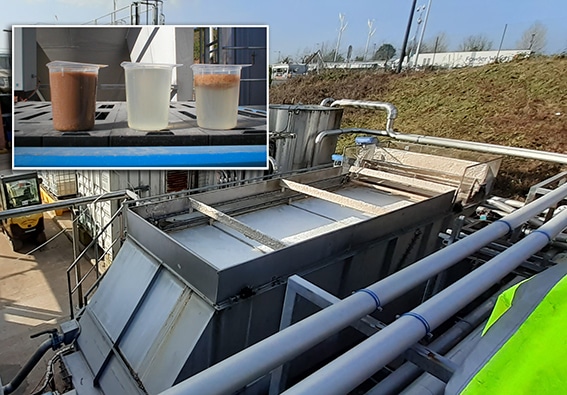
At Muller Market, which produces yoghurt, a MCH30 DAF was installed to treat biological sludge and primary effluent without chemicals.
The use of DAF technology aligns with the dairy industry’s ongoing efforts to minimize waste, reduce environmental footprint, and promote resource efficiency. As the dairy industry evolves, DAF stands as a beacon of change, reshaping conventional practices and fostering a more efficient, eco-friendly, and economically viable sector.